Building the factory of the future
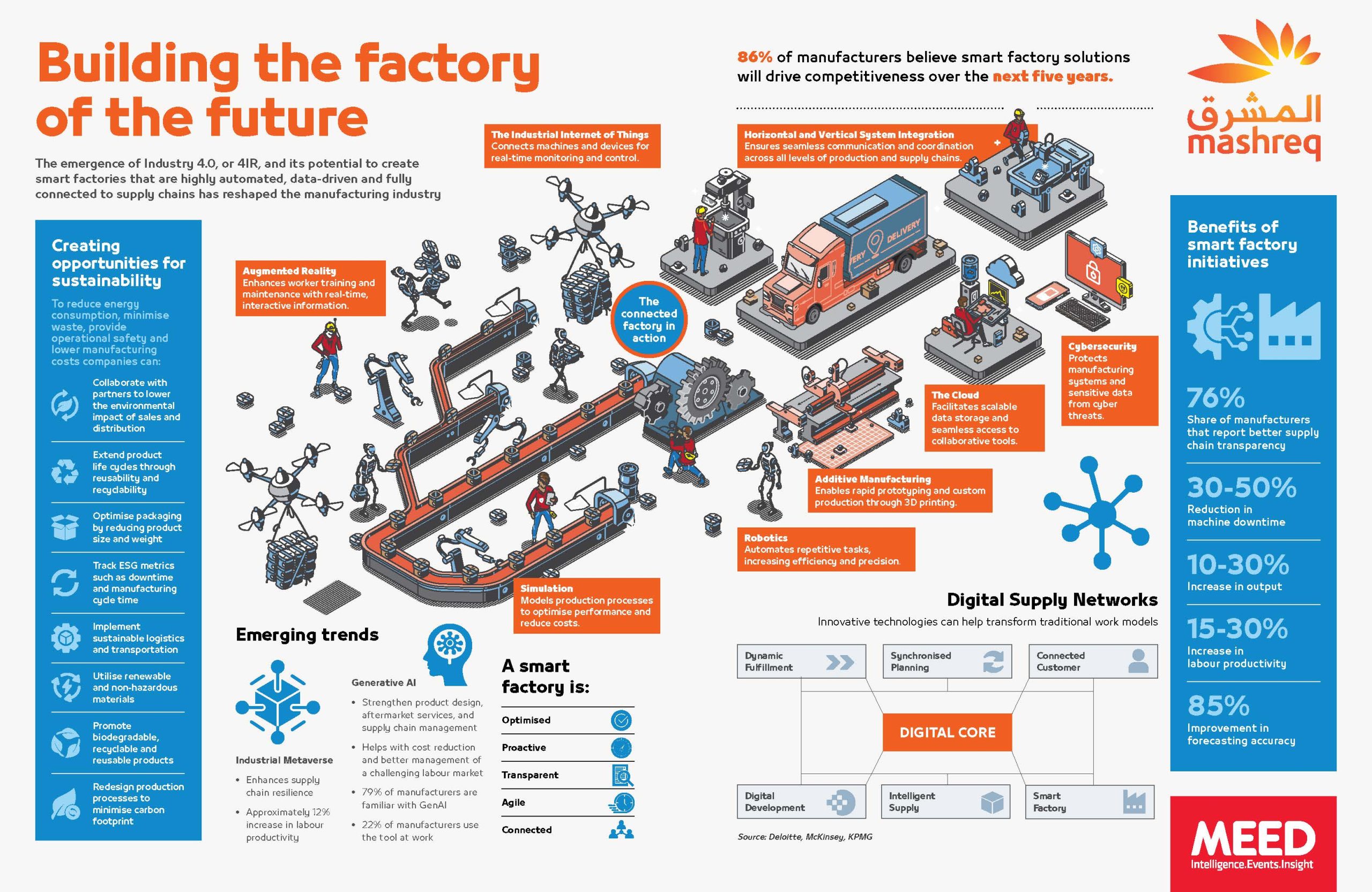
The advent of Industry 4.0, or the Fourth Industrial Revolution (4IR), is revolutionising the manufacturing landscape by introducing smart factories.
These factories are characterised by high levels of automation, data-driven operations, and seamless connectivity with supply chains.
Key technologies driving this transformation include robotics for automating repetitive tasks, simulations for optimising production processes, augmented reality for enhancing worker training and additive manufacturing for rapid prototyping.
Additionally, the cloud offers scalable data storage, while cybersecurity measures protect against digital threats. The Industrial Internet of Things (IIoT) connects machinery for real-time monitoring and big data analytics provides insights for better decision-making.
Horizontal and vertical system integration ensures smooth communication across all production and supply chain levels.
A significant 86% of manufacturers believe that smart factory solutions will be crucial for maintaining competitiveness in the next five years, according to Deloitte.
Smart factories today are defined by their connectedness, optimisation, transparency, proactivity and agility. These attributes lead to substantial benefits:
76% of manufacturers report enhanced supply chain transparency, a 30-50% reduction in machine downtime, a 10-30% increase in output, a 15-30% boost in labor productivity and an 85% improvement in forecasting accuracy, as highlighted by McKinsey.
The shift towards smart factories also brings about changes in workforce skill requirements. Traditional physical and manual skills are decreasing by 30%, while basic literacy and numeracy skills are down by 20%.
Conversely, there is a 50% increase in the demand for technical skills like coding, a 33% rise in complex thinking skills, and a 30% uptick in social and emotional skills. These shifts underline the importance of upskilling the workforce to keep pace with technological advancements.
Sustainability is another critical aspect of smart factory initiatives. Smart factories can significantly reduce energy consumption, minimise waste, enhance operational safety and lower manufacturing costs while promoting environmental stewardship. Companies can collaborate with partners to lessen the environmental impact of sales and distribution, extend product life cycles through reusability and recyclability and optimise packaging by reducing product size and weight.
Tracking ESG metrics, implementing sustainable logistics, using renewable materials and redesigning production processes to minimise carbon footprints are all strategies that contribute to sustainability.
Emerging trends in industrial manufacturing, such as the industrial metaverse and generative AI, offer further enhancements.
The industrial metaverse can bolster supply chain resilience and potentially increase labour productivity by 12%. Generative AI holds promise in product design, aftermarket services and supply chain management, potentially reducing costs and improving labour market management. McKinsey reports that 79% of manufacturers are familiar with generative AI and 22% use it regularly.
Despite these advancements, challenges such as economic disruptions, a tight labour market, rising costs and supply chain stresses remain. However, the ongoing transformation towards smart factories and the adoption of innovative technologies present significant opportunities for overcoming these challenges and achieving sustainable, efficient and competitive manufacturing operations.