Embedding future technologies in your business – Hotpack’s story
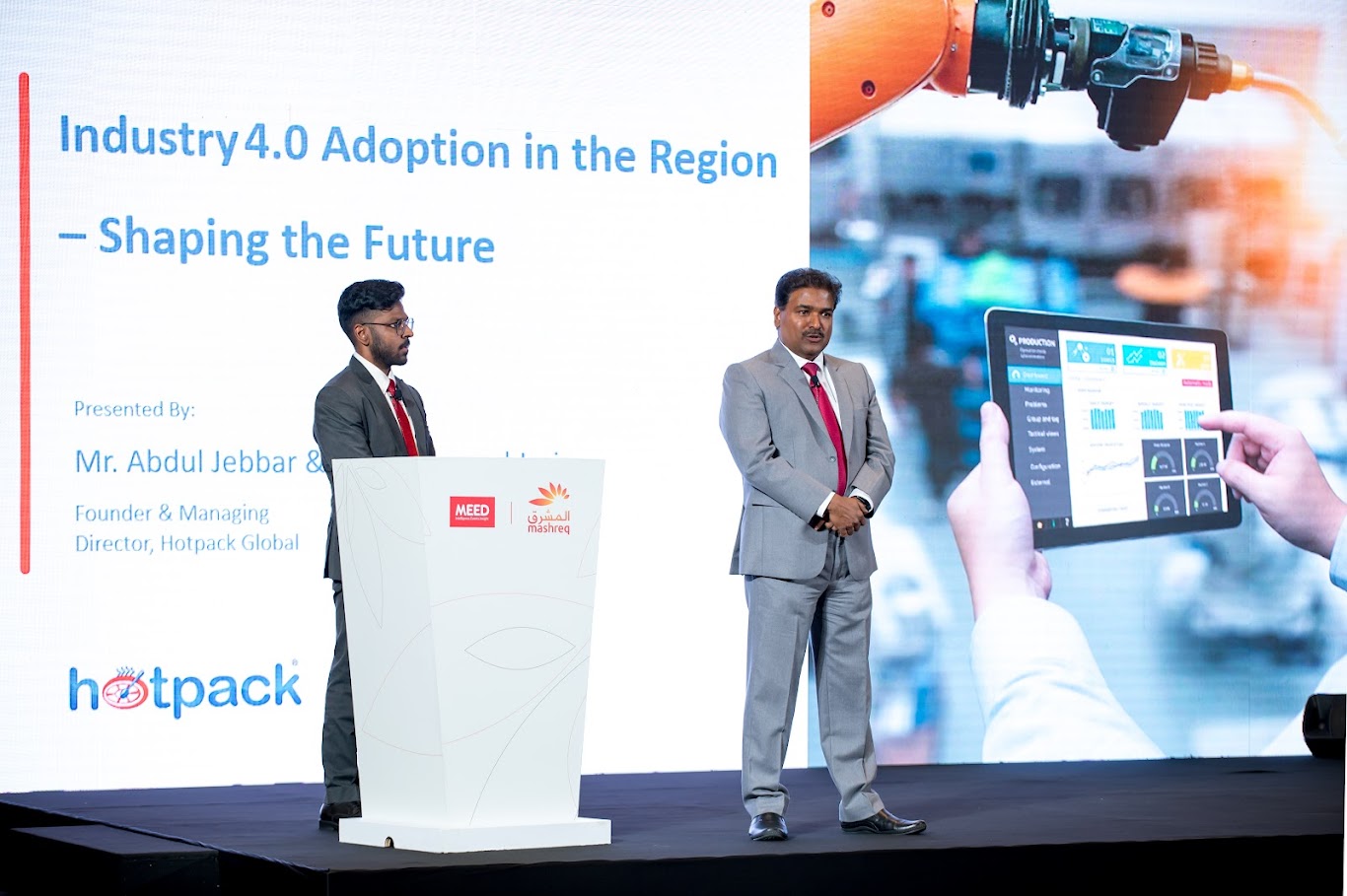
How Industry 4.0 solutions across multiple sites are helping transform operations
Digital and agile work models are changing the way manufacturing industries operate. These models empower factories to become more efficient, responsive and customer-centric in an increasingly competitive and dynamic market landscape.
Hotpack, a UAE-based manufacturer of food packaging solutions, is a notable pioneer. Incorporating digital technologies across its operations has allowed it to increase revenue without raising costs, ultimately improving its overall profitability.
“Technology enables us to compete globally, particularly against countries like China, where manufacturing costs are lower and capabilities are higher,” Abdul Jebbar PB, group CEO and managing director at Hotpack Global, told a recent Mashreq-MEED manufacturing summit.
“Scaling up with technology and reducing costs is the pathway to leadership in manufacturing.”
The challenge
Although companies’ needs for Industry 4.0 differ, Hotpack had been encountering certain setbacks that warranted a digital approach to achieving its short-term and long-term goals.
Manual data collection processes, for instance, resulted in errors during the collection and capturing phases, which in turn created operational inefficiencies. Moreover, the absence of real-time insights into production progress hampered the visibility of the status of products.
A reactive approach to unplanned events also resulted in slow response times and highlighted a lack of agility in addressing challenges.
Reliance on isolated and non-integrated enterprise systems caused further complications due to increasing dependency on results from such software systems.
Added to these issues was a shortage of skilled manpower proficient in utilising advanced technologies, intensifying operational limitations.
Next steps
“Understanding the why, what and how factors of your transformation journey helps you analyse your current position, identify gaps for improvement and provide impactful strategies for progress,” said Mohamed Jasir, assistant vice-president of projects at Hotpack Global.
To kick off its transformational journey, Hotpack launched a pilot programme involving implementing different technologies across its business. These pilots acted as building blocks that laid the groundwork for the organisation’s overarching aim of attaining scalability.
To develop a plan for industrial transformation, the company evaluated its level of Industry 4.0 maturity by using the Industrial Technology Transformation Index (ITTI). This tool enables manufacturers to make informed decisions based on data, allocate resources more efficiently and access financial incentives.
“When implementing technologies, top management must have a clear vision and effectively communicate it with other members of the organisation,” said Jebbar.
“Effective communication is essential to fostering a culture of rapid technology adoption and encouraging people to embrace and use new technologies in their work.”
The next stage involves identifying relevant deployment case studies across the enterprise value stream.
“This targeted approach allows us to identify areas where the most significant impact can be made,” said Jasir.
For Jasir, this expansion aims to improve operational efficiency using predictive technology and enhance transparency with real-time data. Should the pilot fail, Hotpack aims to reassess its strategy before proceeding with future implementations.
With approximately 16 live manufacturing units, the eventual goal will be to emulate the results of key use case studies across multiple sites around the world.
“Global scaleup is the end goal for Industry 4.0,” he said.
During its digital adoption journey, Hotpack recognised inefficiencies in its existing processes and systems, prompting the creation of a multi-year roadmap for business expansion through transformation.
Achieving a 69% score on the ITTI – one of the highest in the region – encouraged a deeper examination of the firm’s operations and the pursuit of additional technologies to improve operational efficiency.
Given its consumer-centric operations, a comprehensive workforce development plan was necessary to transition employees into specialised roles.
Technologies deployed
Hotpack’s pilot project involved using advanced technologies, including programmable logic controllers that were retrofitted onto high-end machines equipped with sensors and meters for data collection.
“By analysing data from sensors, issues with machinery can be detected early, allowing for preventive maintenance to avert further damage or production interruptions,” said Jebbar.
This data was then fed into automated workflows for fleet management and robot-assisted shop floor operations to enhance efficiency and monitor overall equipment effectiveness (OEE) and downtime. Quality inspection was then conducted on the go, with conditional monitoring of machines for predictive maintenance.
“Our next objective will be predictive maintenance using machine learning and predictive analysis for informed decision-making,” said Jasir.
As of today, digital monitoring systems have been attached to manufacturing plants across factories to help detect OEE, downtime and machine status in real-time, allowing for immediate intervention in case of any issues.
Condition monitoring ensures machines operate within healthy parameters, with alerts generated for deviations. The system also generates reports for the maintenance team, monitoring ticket response times and machine performance. Overall, the system enables quick decision-making and proactive maintenance to optimise manufacturing operations.
Jasir emphasises the importance of establishing a baseline trigger to lower consumption and enhance customer experience.
“We have to monitor the baseline and assess the return on investment to drive greater productivity, cost reduction and improved utilisation of assets.”
Looking ahead
Jasir highlighted the importance of Hotpack developing a comprehensive multi-year plan in which incorporating Industry 4.0 technologies is essential to realising its overarching goals.
The successful completion of the pilot programme marked a significant step in this direction, signifying tangible progress towards Industry 4.0 adoption.
“With four manufacturing plants nearing completion, the focus shifts towards interconnecting them and deploying digital solutions across all our operations,” he said.
Looking ahead, Hotpack will prioritise predictive analysis and machine learning, necessitating a systematic evaluation of data quality to leverage advanced technologies effectively.
Additionally, there is interest in integrating immersive technologies, such as digital replicas of machinery, to facilitate a swift response to potential hazards.
Central to this strategy is integrating diverse systems across the value stream, ,aiming to establish a unified platform that provides comprehensive insights for decision-making. This initiative is expected to improve operational efficiency and strategic planning.
Future goals for Hotpack include pursuing net-zero manufacturing and implementing closed-loop autonomous or software systems in its manufacturing units.
Jebbar and Jasir ultimately aspire to attain the ‘Lighthouse’ status, an esteemed recognition within the Global Lighthouse network initiated by the World Economic Forum, which evaluates the future of operations and the impact of Industry 4.0 technologies on production.