The transformative potential of Industry 4.0
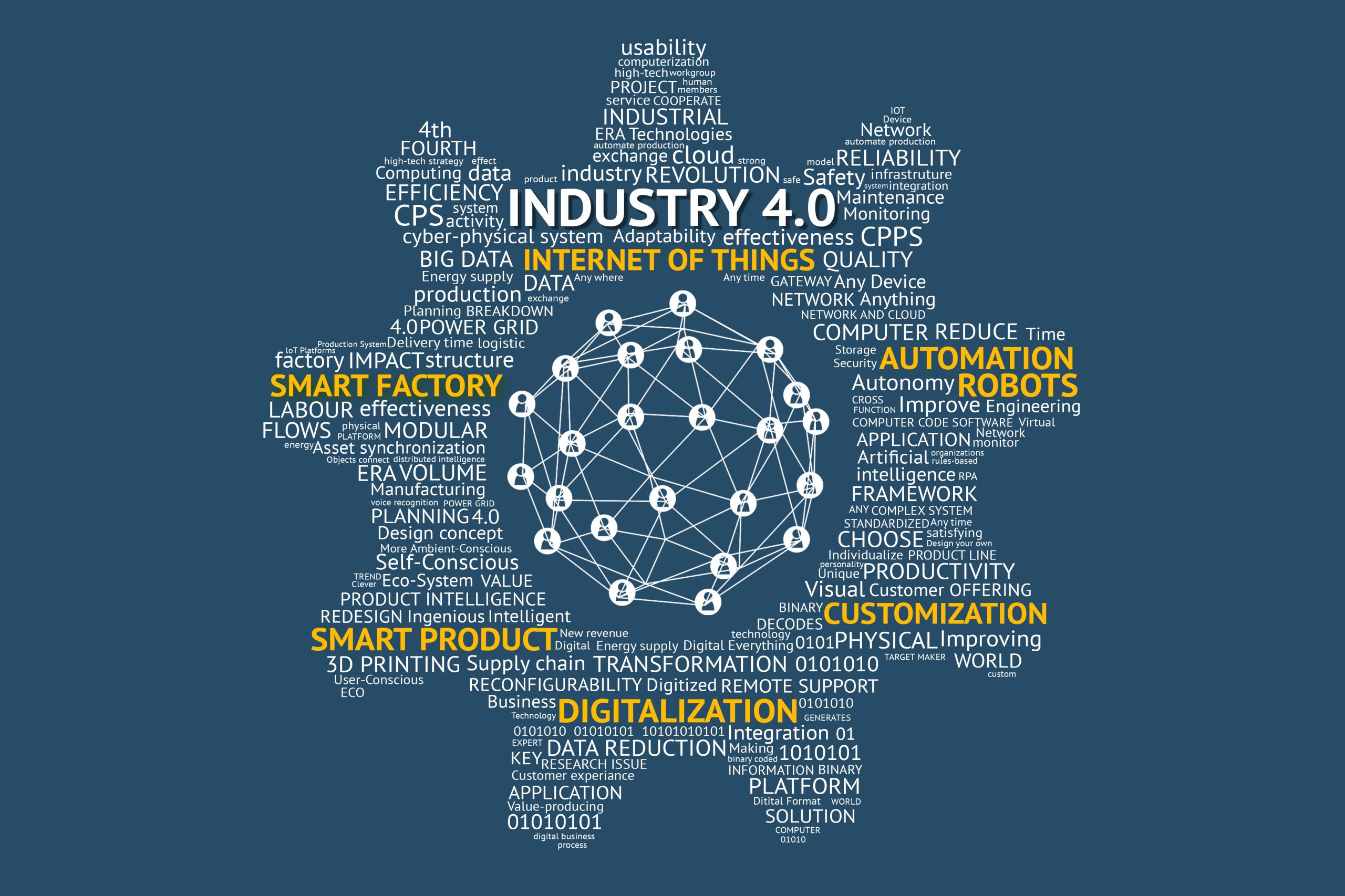
How technological advancements are reshaping production processes and resulting in sustainable outcomes
Digital technologies are rapidly revolutionising all aspects of manufacturing, creating new standards for efficiency and responsiveness.
Dubbed the ‘fourth industrial revolution’ – otherwise known as Industry 4.0 or 4IR – this trend is characterised by the integration of new digital technologies, artificial intelligence (AI) and the internet of things (IoT) into production processes. The result is the transformation of traditional manufacturing processes into smarter, interconnected systems.
“From heightened operational efficiency and flexibility to significant cost savings and rapid market response capabilities, the transformative potential of Industry 4.0 is creating countless new opportunities and business outcomes,” said Umar Khan, senior vice-president of services and manufacturing at Mashreq.
Khan’s comments came at a Mashreq MEED Manufacturing Summit held on 21 February that brought together experts to discuss the significance of integrating newer technologies to streamline existing manufacturing workflows.
Improving efficiency and innovation
World Bank data shows that 80% of companies in the wider Middle East and North Africa (Mena) region are adopting digital technologies. Investment in digital transformation is predicted to rise rapidly, reaching $298.2bn by 2032 from $38.4bn in 2022.
“Digital transformation impacts every business unit and operational process, helping streamline workflows and leverage data-driven decision-making,” said Mohammed Ameen, chief information officer at Masafi Group.
As organisations navigate and adapt to this era of change, the advantages of deploying new-age digital technologies are becoming increasingly evident.
The functionalities of IoT and AI, for instance, empower manufacturers to enhance their understanding of operations by efficiently utilising data and seamlessly integrating diverse systems.
“Collecting data through sensors and monitoring equipment is critical,” said Jay Gadhavi, general manager of the Middle East and Africa at Krohne, a process implementation global company providing advanced electronics and sensor technology. “This data is then analysed using machine-learning algorithms to predict maintenance issues, ultimately improving productivity and reducing downtime.”
The benefits are self-evident. “Data analytics and dashboards provide a clear view of operations, supply chains and key performance indicators (KPIs), allowing for real-time process optimisation based on insights rather than intuition,” Ameen highlighted.
While these data analysing software extract insights from datasets, technologies such as digital twins go a step further by creating dynamic virtual replicas, enabling real-time simulation and analysis of physical entities.
Furthermore, modern sensors can facilitate digital image processing, enabling the assessment of systems and enhancing productivity and efficiency. This includes predictive maintenance, safety evaluations and production overviews using 3D simulations.
This introduction of digital technologies into manufacturing processes has resulted in more efficient, agile and customer-focused supply chains. Connected systems provide real-time visibility into their functionality, enabling better inventory management and responsiveness to changes in demand.
Ultimately, to successfully promote and implement 4IR, companies must assess their readiness to adopt digital technologies and analyse its implications on their business strategy.
Funding digital initiatives
Financial institutions play a crucial role in providing funding to support businesses in their transition to new technologies and the acquisition of modern production assets.
Their assistance enables companies to invest in cutting-edge technologies, machinery and equipment, facilitating a smoother transition to Industry 4.0.
“As financial institutions, we understand the significance of Industry 4.0 and are tailoring structures and frameworks to ease the financial burden on companies,” said Khan.
“Our focus is on understanding how these innovations will enhance the operational efficiency of a business, ensuring companies make the right decision at the right time during the production phase.”
Moreover, banks can share insights and examples of successful digital transformations to help companies make better decisions. These can serve as valuable resources for businesses seeking to enhance their operational efficiency through technological advancements.
Sustainable outcomes
As industries seek to expand and diversify, there is a growing emphasis on embracing sustainability, which is now seen not only as a means to mitigate risks but also as a potential value driver.
Manufacturers are actively exploring ways to cut operating costs tied to production processes by incorporating technologies aligned with sustainable practices.
“Industry 4.0 is about heightened efficiency, improved output and reduced waste, which could contribute to greater economic development and growth through improved operational efficiency,” said Yousra Elsayed, director of sustainable finance at Mashreq.
A transition towards a circular economy framework, upon better understanding their current impacts across the value chain, can help manufacturers establish a baseline and identify opportunities to reduce and recycle.
By minimising waste and water consumption, optimising energy usage and harnessing renewable resources, factories have the potential to drive measurable sustainability outcomes and reduced costs.
Additionally, to achieve their sustainability objectives, it is essential for companies to have a sustainability roadmap of projects, activities and initiatives that guides them to achieve their net-zero goals.
“Leveraging Industry 4.0 technology enables companies to attain genuine net-zero outcomes, grounded not in broad assumptions but in precise measurements,” said Mike Cheetham, head of sustainability at Hotpack Packaging Industries.
“Companies must consistently reevaluate their KPIs along the roadmap, find the gaps and design solutions to achieve the desired outcomes.”
While sustainability is rapidly gaining traction in the manufacturing sector, companies embracing these practices are not only improving productivity and cutting costs but also distinguishing themselves from competitors, positioning themselves to stay ahead of regulatory changes.
Addressing challenges
From assessing existing assets, determining compatibility and looking out for any threats before they become significant problems, the process of transformation varies among different companies.
“For newly established companies, the process is relatively simpler than the extensive groundwork required by legacy companies,” said Ameen.
New companies have the advantage of starting with a clean slate, enabling them to build digital and smart technologies into their operations from the outset, while legacy systems may lack the scalability needed to accommodate the demands of the modern business environment.
Additionally, any change requires active participation from everyone within the organisation.
“Navigating cultural change is a hurdle when transforming legacy companies. Support from all stakeholders is needed to overcome resistance to new technologies and work practices,” said Shakti Arora, chief procurement officer at RAK Ceramics.
Therefore, fostering a culture of continuous learning and equipping employees with the essential tools will help streamline tasks and enhance collaboration, as well as empower them to maximise productivity and leverage real-time data.
This will then ensure sustained growth and competitiveness in the ever-evolving business landscape.